Chains, sprockets
General information
One of the defining and frequently used elements of industrial drive technology is the roller chain. Although very strong toothed belts are now available for positive shift drives, the roller chain is so widespread in industry, automotive and agriculture that its use is expected for many decades to come. The advantage of chain drives is that relatively large forces can be transmitted without slip even on a sprocket with a small diameter. Since chain drives have been in service for many decades, we can talk about mature, reliable technology.
The basic elements of chain drives are roller chains and sprockets. In addition, additional elements such as chain tensioners, chain guides, chain assembly tools, etc. can be used... Roller chains can be made of stainless materials, but so-called lug chains can be made of roller chains, which can perform transport functions. But we know of bartender chains, where the connecting pin sticks out of the chain on one or even both sides. We know pipe pin chains, where the pin connecting the links is not solid, but tubular. We know stretched chains, etc., etc...
Most roller chains used in industry are manufactured according to a standard developed by a major standard agency (ISO, ANSI) or as a further development of a standardized roller chain. Chain drives used in Europe basically use roller chains in accordance with ISO (BS) standard. A typical roller chain of American-origin machines is the ANSI (ASA) standard design. These chain standards are very similar to each other, but roller chains of different standards do not match! Their interchangeability shall be checked individually each time. In addition to the two main standards, there are also roller chains developed for various industrial purposes and previously standardized in another country (e.g. JIS1801, ISO1395C, etc.). Roller chains can only be used with their own sprockets. In general, you should not change the type of chain without replacing the sprocket, do not use chains and sprockets of different standards. Or, in such a case, expect premature wear of the roller chain or sprocket.
In the case of sprockets, it is always decided by the mounting possibilities of the given application whether a sprocket or a hub sprocket should be used. Bevel clamping sprockets are essentially special hub sprockets that can be installed in the machine with a tapered clamp without performing machining work. The bearing, tensioning lens wheels are mounted between two or more sprockets to maintain the tension of the chains and prevent elongation and tooth jumping. The tension sprocket is usually fixed flexibly to follow the already created chain elongation. For sprockets, there are toothhardened and non-hardened versions. To put it simply, if you use a sprocket with hardened teeth, there is a good chance that the roller chain will wear out faster. If you use a sprocket without tooth training, the sprocket is likely to break first. Which design to choose should be modeled by engineering calculation. In the absence of this, decide whether it is easier to change chains or sprockets on your equipment and choose sprockets with hardened teeth or untrained teeth accordingly... When choosing roller chains, it is necessary to take into account the available space, the torque transmitted, the place of use and the conditions of use. If you want to use the roller chain not only for moving, but also for lifting, you must pay attention to tensile strength and elongation! Although chains are relatively easy to assemble, their selection may require knowledge. If necessary, seek professional advice. There are very tiny roller chain designs called miniature chains. We do not recommend using them, they can be perfectly replaced by using a toothed belt! (By the way, reinforced toothed belts, e.g. Megadyne Gold, Megadyne Platinum or Megadyne Titanium, are also suitable for replacing roller chains of very serious size. Quieter, cleaner, quieter...)
News
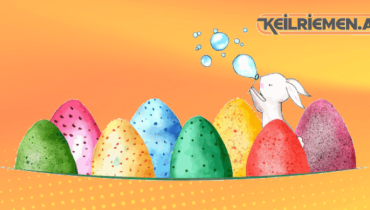
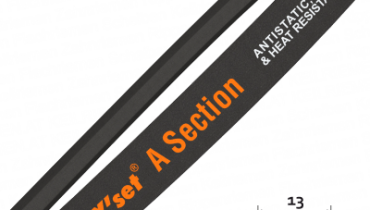
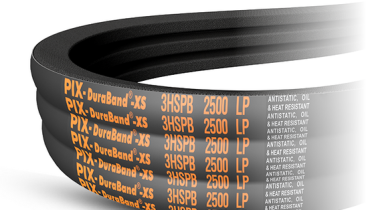
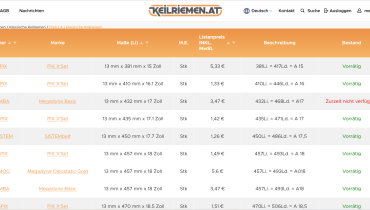